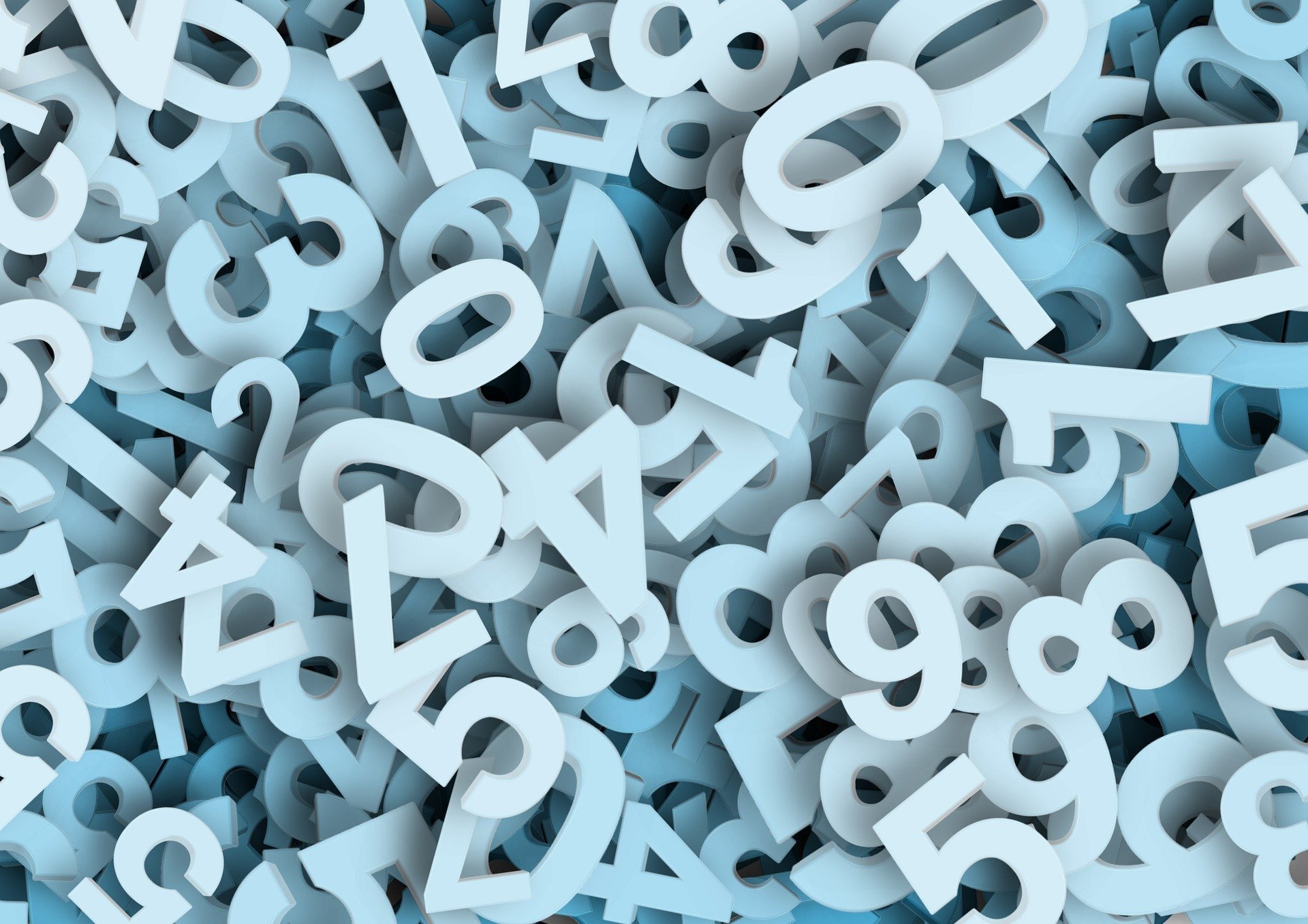
Why you should base your Part Numbering System in PLM and not in CAD
We previously defined what constitutes a ‘good’ Customer Part Number format, but now we will address where the Part Numbering System should originate.
When building your hardware products and associated BOM (Bill of Materials), a Customer Part Number (CPN) is an industry best practice for uniquely identifying each component. While the Part Name may also be used as a reference, the CPN is the default reference used by professional hardware manufacturing teams. While every hardware company is entitled to select which tool will be used to generate the number, it is standard for the CPN to be auto-generated by a CAD, PLM, ERP or IMS tool. Each option has its merits. Below we’ll explore why a Part Numbering System based in a Product Lifecycle Management (PLM) system is a superior option to a CAD-based Part Numbering System.
Duro is an award-winning cloud-native Product Lifecycle Management platform incorporating best practices for part numbering.
Schedule a demo to see how Duro can help your team.

The initial hardware product definition for number generating software almost always comes from the engineering department. Engineering team members will define the main characteristics of some item or system by classifying the component parts and generating the initial Bill of Materials. It is not uncommon for initial part numbering efforts to fall within the engineer’s domain and even be manually managed by a simple spreadsheet. CAD systems, like Onshape, provide design teams with a means of deploying a Part Numbering System in the early phases of the design process, as the Bill of Materials is taking shape. A CAD-based Part Numbering System is a great way to get started but introduce a number of down-stream risks.
One major risk is simply the presence of other CAD tools used throughout the organization. Multiple CAD tools necessitate a merging of design work into a central hub. Uniquely identifying each component within its originating CAD tool becomes a burden as components are merged into a common Bill of Materials from multiple CAD sources. A PLM tool provides both a means of merging work content from disparate engineering design sources as well as managing a Part Numbering System that can, in many cases, be pulled back into each CAD tool. Duro, as an example, can normalize all part and assembly data with consistent part number management software, naming, and revisioning; making for a smoother transition into production. It empowers engineers to get to production at the lowest cost and highest efficiency.
To learn more about Duro, schedule a demo here.
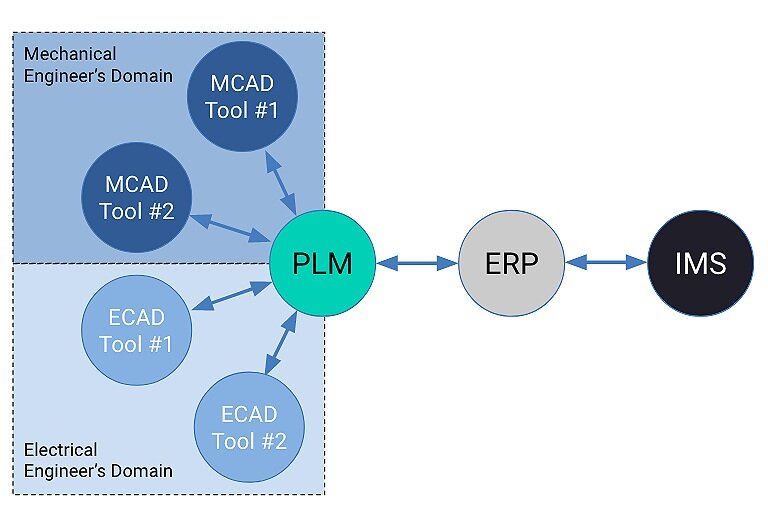
A Part Numbering System based in a CAD tool is often initiated without taking into account how the system will work with the other disparate, but equally critical business and manufacturing tools downstream of CAD. For instance, with the implementation of an ERP system using product lifecycle tools a company may begin managing part numbers from different suppliers and manufacturers. Aligning these external part numbers with internal part numbers originating from a CAD system has the potential to introduce not just miscommunication but even manufacturing delays.
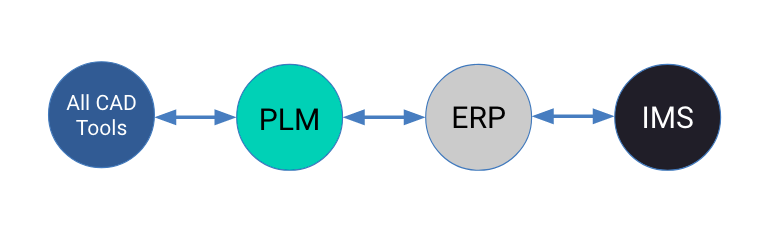
Ideally, before the product development lifecycle moves into design, the entire organization would adopt a system external to all CAD tools to centralize the Part Numbering System and provide a means to pull the part numbers into any and all CAD tools. A PLM tool’s part numbering capacities can make it easy to centralize the Part Numbering System, prevent conflicts with external part numbers, as well as navigate multiple Bills of Materials. Ultimately a PLM-based Part Numbering System is the emerging industry best practice for centralizing part numbering across teams’ tools and avoiding costly downstream issues for ERP or IMS.