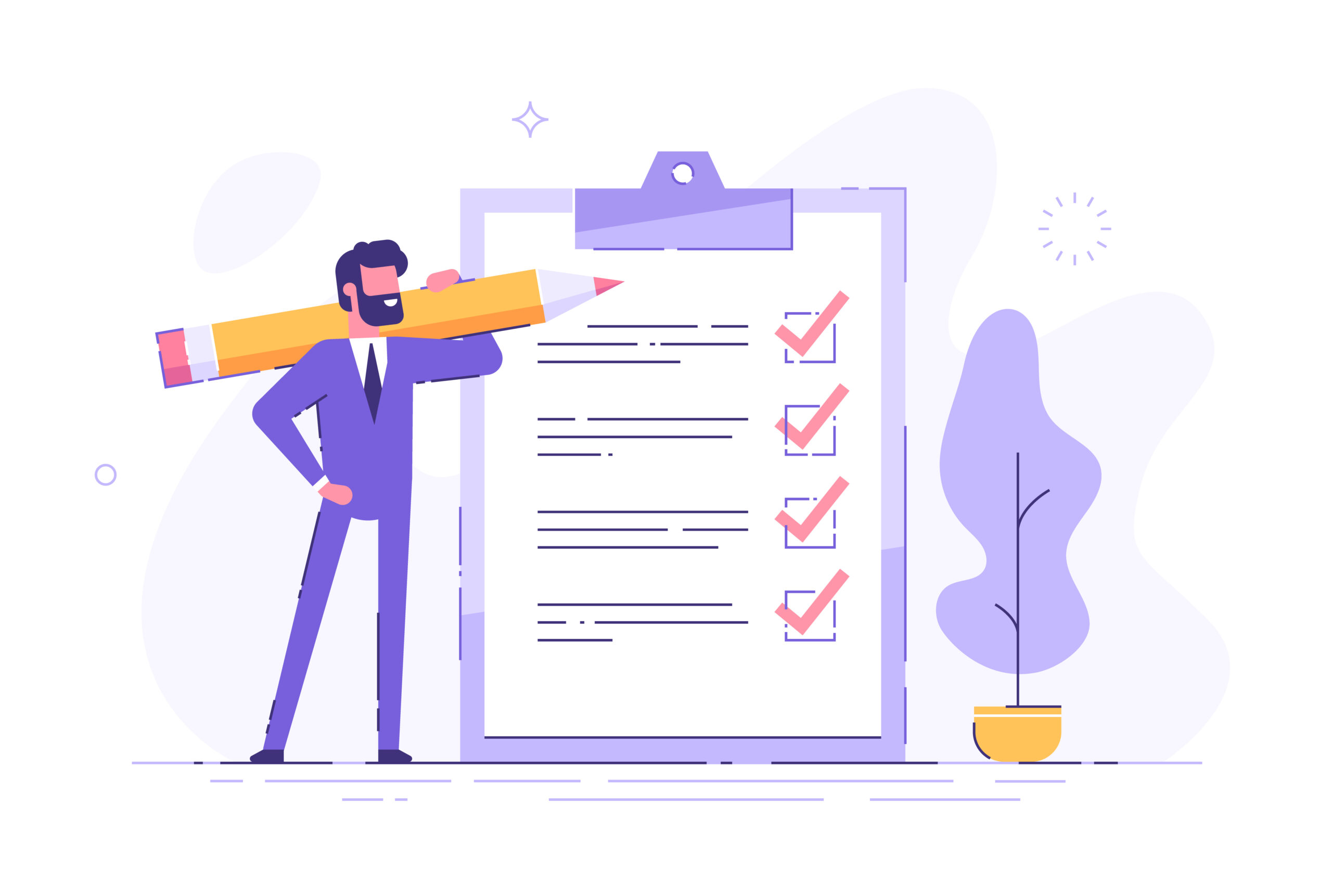
The Ultimate Engineering Change Order Checklist
Engineering Change Orders are hard — let cloud PLM do the work
Sophia Barnett, Content and Technical Writer
Product development is rarely a linear process. Even with the most meticulous planning, issues can crop up once a product design moves from the drawing board to the manufacturing floor. That’s where Engineering Change Orders (ECOs) become indispensable.
ECOs are formal documents that outline and authorize necessary changes to a product’s design, ensuring problems are resolved swiftly. ECOs can address unexpected challenges derailing a product launch or creating ongoing headaches. Here are common problems ECOs are designed to solve:
- Unforeseen Costs: ECOs can facilitate design adjustments to bring costs back in line when production expenses exceed those outlined in the budget.
- Defective Products: Product defects uncovered through customer feedback, warranty recalls, or quality control testing can be addressed through an ECO to realign product integrity.
- Shifting Resources: If materials or components become unavailable, ECOs provide a framework to implement substitutions or alternative designs.
- Compliance Breaches: ECOs document modifications for regulatory compliance (ITAR), support traceability, submit records to auditors, and address updates to meet new standards.
Engineering Change Order benefits
Effective engineering change management starts with an error-free Engineering Change Order (ECO). Change Orders are complex, but with cloud-based PLM (Product Lifecycle Management) software and agile workflows, they don’t have to be time-consuming or frustrating. Cloud PLM streamlines processes, automates tasks, and provides real-time collaboration, making ECOs a smooth part of your product development.
Avoid errors in product development
Updating your product library via ECOs helps you catch errors early, reducing the likelihood of issues happening down the line in both manufacturing and inventory. ECOs streamline collaboration by creating a central source of truth for everyone involved in the process. They help with cost control, keep your projects on schedule, and ensure product information is always up-to-date.
To that effect, we developed a custom integration with Tulip to help reduce errors, create consistent documentation, and promote data sharing between PLM and your production floor.
Faster time-to-market
Engineering change orders boost your company’s competitive edge through faster time to market (TTM). They provide a structured system for handling design adjustments during a product development lifecycle.
ECOs empower teams to communicate clearly and collaborate, ensuring everyone is on the same page. These mid-course corrections prevent costly late-stage redesigns and wasted resources. The result is a faster time to market, giving your company a competitive edge.
What is an Engineering Change Order?
Engineering Change Orders are formal documents that propose alterations to a product’s design, components, processes, or documentation. Errors, design improvements, component obsolescence issues, regulatory compliance needs, or customer requests can trigger these changes at any point in the product development lifecycle.
An up-to-date and error-free ECO process helps manage changes effectively. Engineering, production, quality control, and other departments must collaborate to carefully evaluate potential impacts.
ECO process
Engineering change orders are the heart of revision management. A strong ECO process enables teams to identify, evaluate, and approve modifications swiftly. ECOs are commonly used to quickly identify form, fit, or functional changes made by an engineering team. To submit an ECO for approval, it must have a name value, a description, at least one product or component added, and a specified approval type.
Engineering Change Order example
An Engineering Change Order in Duro has several key components. This ECO form includes a name field for a title, a detailed description section to outline the change and its implications, and tabs for products and components, approvers, and notifications. The products and components tab allows for adding items to the Change Order, with options to include parent or child assemblies, showcasing the current and new revision values and status updates.
In this ECO process, initiators can choose how approvals happen, with the following options: first-in, majority, or unanimous decision options. The notification list informs internal and external parties of the outcome of the change order. The ECO form facilitates a validation process to address potential issues before they arise. With Cloud PLM software, ECOs can be in draft, open, or closed status, each allowing for different levels of modification and approval actions.
Two ECO phases during the release workflow
The ECO workflow is structured into two distinct phases, each characterized by its own set of approvers and unique workload requirements.
First ECO phase
The first phase of the change approval process focuses on how the change impacts product design and function. Design engineers and their managers are the primary approvers, with potential input from manufacturing experts for feasibility assessments. This phase can often be handled within CAD tools with release management features or a dedicated PLM system.
Second ECO phase
The second phase shifts the focus to how the change affects manufacturing processes, schedules, costs, and overall business operations. Phase two involves a more diverse group of stakeholders. Unlike Phase 1, rejections in Phase 2 may not require complete design rework. This stakeholder group can resolve approval requests if the design isn’t impacted. Ideally, we recommend using a PLM system for this phase because it offers broader access and visibility.
Engineering Change Order use cases
Let’s say your company develops drones. But, the propellers on the drone (we’ll call it the Hexacopter Drone, or Model HX-350) are failing under high-stress conditions, posing a risk of crashes and potential harm. An engineering change order is needed to propose and implement design changes to address the issues.
This redesign will incorporate a stronger composite material, increase blade root thickness, and optimize blade root geometry for improved stress distribution. The ECO process will ensure these changes are carefully designed, tested, and integrated into production.
Furthermore, it will update all relevant technical documentation to reflect the improved propeller specifications. This ECO is essential to ensuring the drone’s safety and reliability in the future.
Engineering Change Order process simplified
A typical ECO undergoes a seven-stage journey before approval and implementation. Providing complete, well-organized, and easily understood information within your ECOs will increase their chances of swift approval and streamline the resolution process.
- Determine if there’s a need for an ECO
- List the reasons the change is needed
- Start your engineering change order
- Review the ECO
- Select approvers and submit the ECO to them
- Notify relevant stakeholders via Slack
- Upon approval, implement the change
How Engineering Change Orders promote consistency
Implementing a standardized engineering change order process helps to maintain consistency across projects. This structured approach ensures quality control and reduces errors by capturing all high-level information for each change and structuring approval workflows to prevent unauthorized modifications. This ECO process provides a transparent view of changes and utilizes consistent terminology to minimize confusion and misinterpretation.
On top of that, ECOs eliminate the need to set up procedures for each change, enabling faster approvals and implementation. They support the creation of a historical record and audibility by tracking all changes with their key details for future reference. An engineering change order serves as a knowledge base for informed decision-making.
Engineering Change Order checklist
Your primary objective is to secure approval for your ECO and eliminate the cycle of repeated kickbacks, adjustments, resubmissions, and approvals. Here are a few best practices to streamline your ECO process:
- Clearly articulate the description of the change.
- Include a thorough analysis of the impact on assembly, rolled-up cost, and lead times.
- Determine and document the root cause of the issue prompting the ECO.
- Ensure the notification and approver lists include all relevant stakeholders.
- Keep the change orders clean and manageable.
- Define a clear scope for the change order, avoiding unnecessary complexity.
- Refrain from merging multiple updates within the same change order.
- Maintain consistent documentation throughout the process.
Bonus tip – let Cloud PLM automate action items
Perhaps the biggest benefit of automated notifications is that they allow you to stay up to date at all times. The system automatically updates the status of an engineering change order, eliminating the need for manual checks. A good example is integrating PLM software with Slack to inform users of actions taken on ECOs such as submissions, approvals, and rejections. Integrating automated notifications on change orders with a Slack channel offers several benefits.
PLM Slack integration benefits
A PLM Slack integration creates a centralized communication hub for an engineering team, providing easy access to essential links, resources, and required actions. In addition to these benefits, the integration enables stakeholders to receive quick, high-level updates on the status of change orders without navigating between platforms.
This integration promotes transparency and keeps everyone informed. Ultimately, this approach to automated notifications fosters enhanced collaboration between the engineering team and stakeholders, leading to better alignment and more efficient decision-making throughout the ECO process.
Get your ECOs right from the start and avoid mistakes
ECOs can be complicated, but they don’t need to be. Cloud-based PLM software and agile workflows can do the work for you – and save you and your team a lot of time in the process. Using a PLM with predetermined agile workflows to manage ECO processes ensures they are an integral and streamlined part of your product development lifecycle.
The right PLM can provide real-time collaboration and automation to prevent errors and align product design with manufacturing and inventory requirements. Using PLM software for ECOs fosters efficient design adjustments and collaboration, reducing late-stage redesigns and resource waste.
Simplify your ECO process and streamline product development – let’s chat about how our cloud-based PLM solution can help.