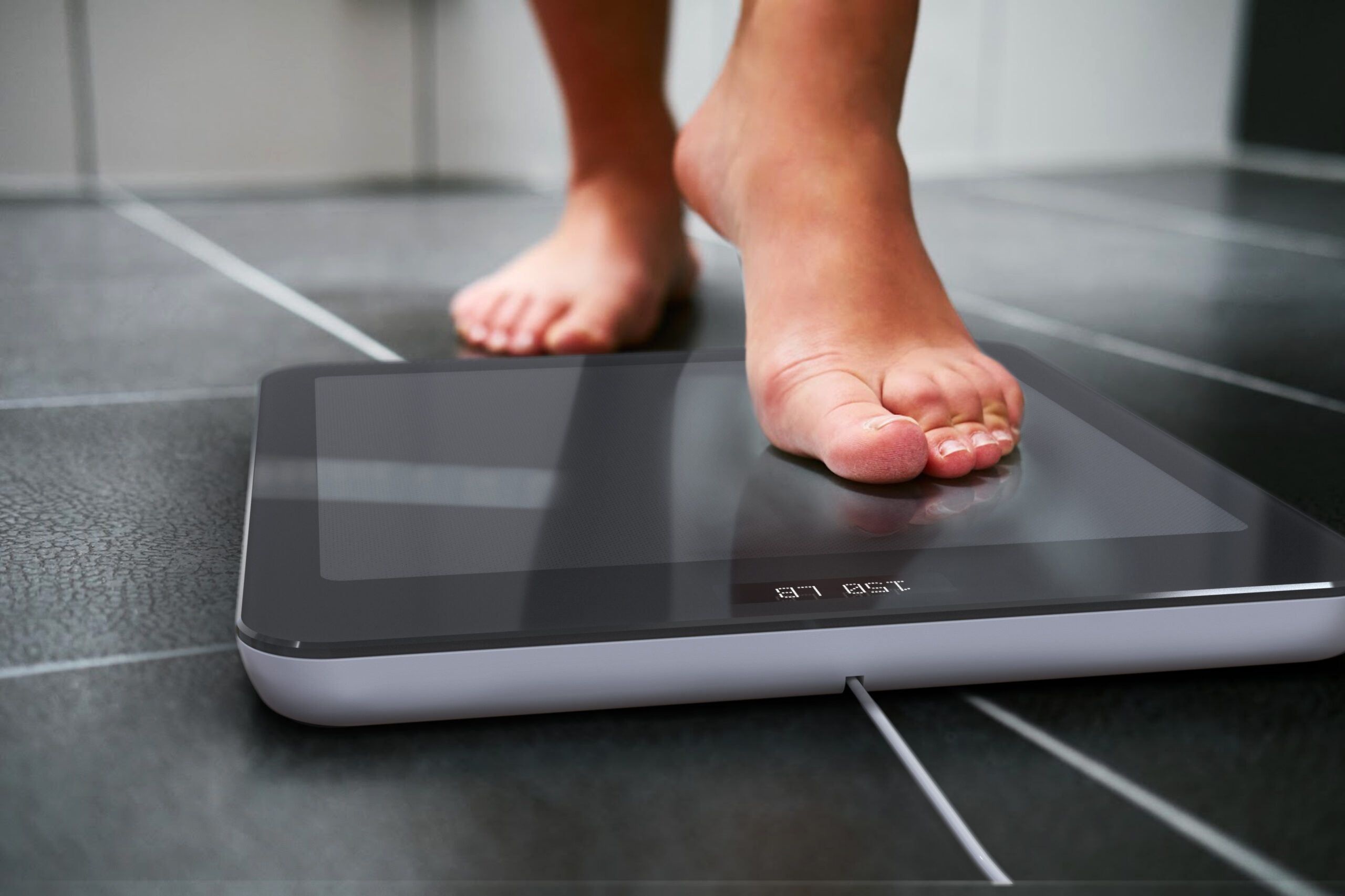
Customer Spotlight: Why Empo Health invested in PLM before they Hired an Engineering Team
We love hearing about the cool products our customers are building and how Duro transforms their work. This article is part of our Customer Spotlight blog series, where we interview engineers using Duro and share their stories with you.
Over a quick conversation with Empo Health’s Co-Founder Eric Dahlseng, we learned that PLM was an early priority as they built out their tech stack. Eric shared more about why he’s building a product to help manage diabetes and which new technology makes this possible.
What are you building at Empo Health?
We’re developing health monitoring devices that would be used in homes by patients focusing on chronic disease management. Our focus is specifically on diabetes, and our first product is focused on diabetic foot complications. Our smart scale will help track the health of a diabetic patient’s feet to help them and their doctors catch early signs of issues that might develop. It’s a common complication for patients who have diabetes.
What’s your role there and how has it changed?
I’m the Co-founder and Chief Product Officer and I lead product strategy and development. Anuj Khandelwal and I co-founded Empo Health 3.5 years ago. At the very beginning, we were doing a lot of doctor and patient interviews to make sure we really understood the needs of our patients, and then from there, we worked backward to figure out which product would best satisfy that need. Today, we’re a team of around a dozen people spanning both engineering and clinical research.
What makes your product unique?
Because the scope of the issue is so large, there are a number of other companies and products out there that focus on this problem too. But what we’re really focused on is visual imaging specifically. Visuals provide a lot of context for doctors and patients to understand what’s going on with their feet.
Why hasn’t something like this been built before?
It’s very challenging to design a product that can capture visual data from the bottom of someone’s feet while supporting the full weight of a person, and also fit in a form factor that can comfortably fit into a home. It’s taken our team a lot of technical innovation to be able to satisfy all of these constraints. On top of that, the IoT infrastructure needed to be able to support the amount and types of data that we’re capturing didn’t exist in a practically usable way until relatively recently.
What stage in product development are you at?
This device isn’t commercially available yet. We’re still in the product development stage, working on clinical studies. We’re validating our product with patients to make sure that we’re developing a product that will fit into the care cycle for doctors and their patients. We’re looking to begin commercialization in 2024.
How do you address collaboration between Engineering and Clinical Research?
We place a big focus on constantly communicating results. Every week, we share the latest learnings from the clinical studies and user tests that we’re running. As soon as someone from the clinical team learns something from the studies they’ll post that internally in Slack. Staying on track with solving user needs always drives requirements and what’s next for the product. We document every requirement, capability, and specification as well as metrics to hit in a clinical study.
What does your tech stack look like?
We use Slack regularly for communications and we use Google Workspace for our internal documents and communication. For software development, we use GitHub and Linear. For hardware development, we use Onshape for our mechanical CAD work. We made a choice very early on to make sure that any tool we chose provided easy, modern collaboration and supported users on different machines. That’s how we started with our tech stack.
We started pretty early with our PLM system. Before we had fully grown out our engineering team, we evaluated and purchased Duro.
Why did you decide to purchase a PLM platform straight away?
We design a prototype, and then we have to build multiples of them to be able to put those into studies and tests. Other types of early–stage teams might be able to build a handful of units at a given prototype stage, run some lab level verification and testing, carry out smaller scale user tests, and then move to the next stage. However, we had to build several dozen functional units to put into a longer-term study and then learn from that.
It’s so much easier if we have a Bill of Materials with a part number for everything that we’re building. That way, we can clearly understand the quantities of everything that we’re ordering, and if there are multiples of components, be able to do roll-ups in our assemblies so that we can place orders for everything that’s needed. Without a PLM system in place to assign part numbers or calculate component quantities, that can get messy, really quickly.
With a small team, we want to avoid sitting down and trying to build something and then realizing we didn’t order enough or forgot a component. We don’t have time to deal with the delays that come from missing things. And so we wanted to complete this in one shot and then move on to the building part.
Duro allows us to minimize the time we spend doing rote tasks and documenting our designs (an important and required part of medical device development) so that we can provide value and build our product.
Have you read or listened to anything great recently?
I recently read the book Project Hail Mary by Andy Weir and loved it! It’s a beautiful story about science, engineering, and (surprisingly!) friendship.
Tell me a fun fact about Empo Heath
We built the first prototypes, almost 50 units, in a garage! It’s not trivial to build 50 units of anything early on. We spent many late nights, building things by hand, finding enough space to store everything, and struggling to keep the garage warm with space heaters while we performed finer electrical tasks.
It was a big focus for us to make sure that we built consistent prototypes for the user tests. That’s why we ended up with PLM earlier in the process to help support us through that.
Over time, we’ve built a number of prototypes for a variety of user tests and studies. Each one focused on validating a different part of the product and design. The product concept has evolved and matured in response to feedback and learnings. Now we have late-stage prototypes (built in our lab, not a garage!) in clinical studies as we work on the finishing touches before commercialization.